Jan 12, 2022
Predictive maintenance goes one step further than preventive maintenance, by actively predicting when something is going to happen before it does.
Benefits of Predictive Maintenance include reduced downtime, lower operating costs and improved reliability. Examples of predictive maintenance include vibration analysis, ultrasound testing, infrared thermography and oil analysis. These technologies provide early warning signals that can be addressed proactively.
What does predictive maintenance mean?
Predictive maintenance is also called condition-based maintenance and is used to monitor the performance of machines while they are running regularly and reduce the chance of breakdown. Manufacturers started making predictive maintenance plans around the early 1990s.
How does predictive maintenance work?
Predictive Maintenance uses historical and live logging data on various aspects of a business to identify and avoid issues. IoT and Artificial Intelligence also provide a new means to connect and share data for predictive mainenance.
What are the benefits of implementing predictive maintenance?
Reduced Maintenance Costs
Preventative maintenance can reduce maintenance costs. It becomes especially important if organisations must pay for labour maintenance, parts replacement, tools and equipment in case of a catastrophic breakdown.
Fewer Machine Failures
Several studies have been done to reduce machine failures. Regular system monitoring helps reduce unexpected failures. After two decades of implementing predictive maintenance, machines often fail less frequently than expected.
Improved Machine Performance
Predictive maintenance helps to identify and resolve issues before they become problems. This can lead to improved machine performance, lower electricity costs, higher production rates and improved quality of product produced.
Reduced Downtime
Equipment downtime results in lost opportunities for the organisation which could result in lost profits and losses in customer
Increased Lifespan of Machinery
Detecting machine problems is crucial to increase its life expectancy. A predictive maintenance program is essential to ensure equipment cannot become damaged. Longer lifespan guarantees better returns on invested investment in organizations.
Why is predictive maintenance in manufacturing?
Predictive maintenance is the maintenance which monitors asset health status in real-time. Predictive maintenance can reduce costly unexpected breakdowns if compared to a standard routine maintenance program. It also increases uptime, reduces cost of maintenance and improves quality.
Predictive maintenance helps with the prevention of small problems from becoming major ones which could otherwise result in costly repairs or replacements. It is especially useful in manufacturing where time-sensitive products require precise production schedules and machinery reliability can be paramount to success.
By having an understanding of how often equipment needs to be serviced, predictive maintenance can help plan accurate scheduling and reduce risk of disruption in production. Additionally, it optimizes resources and capital expenditures by helping reduce unplanned downtime and inventory costs.
Overall, predictive maintenance is the key to success for any modern manufacturing company aiming to stay competitive and maximize profits.
How do you collect data for predictive maintenance?
Three commonly used techniques in data collection include electro mechanical, thermal, and oil and gas testing. Create machine learning algorithms. Use the information collected during this process to create an algorithm to help you predict equipment failure. Use of IoT systems and sensors is also a popular way to detect any changes in equipment performance. With the right setup and data, predictive maintenance can provide powerful insights into your manufacturing operations.
By monitoring machine performance data, you are able to proactively identify potential problems before they occur and take corrective action. Investing in preventive maintenance activities such as calibrations and repairs can save you costs and productivity in the long run. With predictive maintenance, you can also improve the safety of your facilities.
IoT-enabled devices can provide real-time updates on machine performance and alert you to potential hazards or hazards before they occur. Lastly, predictive maintenance helps reduce downtime, resulting in improved production outputs and increased revenues.
Monitoring and industrial analytics tools
Industrial analytics have become part of a large part of the Fourth Industrial Revolution. It focuses on the convergence of traditional industry practices with technological advancement. Among those advances is the use of machine learning to perform statistical analyses and to interpret the results, as well as the introduction of connectivity through IoT.
What this really translates means is that decisions and actions have started to depend more heavily upon measurable data to act quickly and effectively. A key component in each of these fields includes sensors that monitor key components.
Machine Learning for Predictive Maintenance
The role of machine learning for predictive maintenance is to monitor equipment, detect anomalies, and alert users before significant damage occurs. This can be done by collecting a variety of data sources such as vibration sensors, temperature sensors, and pressure sensors. Data collected from these sources can then be used to determine a baseline for normal operation. If the data falls outside of that range, it is flagged as an anomaly.
Machine learning algorithms can be used to continually monitor these anomalies and alert users when an out-of-range event occurs. This allows maintenance teams to take preventative action before equipment damage becomes an issue.
Examples of machine learning for predictive maintenance are found in the predictive maintenance of aircraft engines, ships, and even medical equipment. By analyzing data from sensors, machine learning algorithms can detect issues that may not be noticeable to human operators. This allows for timely intervention to reduce downtime and decrease repair costs. Predictive maintenance can also help to increase safety by preventing accidents caused by malfunctioning equipment.
IoT sensors
Sensors are always a vital part of every predictive maintenance programme as they enable us to monitor tiny changes and correct these accordingly. Multiple sensors can provide you with a more accurate and reliable way to monitor processes and to prevent early failure and subsequent downtime. Any sensor you require to be successful is advisable to be careful when using it when implementing a project with other sensors or other equipment to achieve this task.
Sensors measure various components of the machine, including temperature, pressure, noise, etc. In the infrared space, the sensor is used for the comparison between temperature differences between a component. Through IR technology, ir sensors can pinpoint current or future problems in varying assets and materials. Through a variety of light sources that are invisible to the naked eye, the sensor identified a substance for the temperature. IR is capable of measuring temperature differences in a single view and in multiple views.
Infrared Thermography
Infrared thermography provides low-response testing techniques using the infrared spectrum. The camera can be used to monitor the temperature at the equipment's highest. Components that are worn out or lack circuitry can start heating--which appears in a thermal image. Infrared inspections can detect hot spots and fix equipment to prevent bigger problems. Infrared technology provides versatility for many different machinery and infrastructure applications.
Acoustic Monitoring
Acoustic surveillance enables maintenance personnel to detect gases and liquid leakages in the piping at the atomic and ion levels. Ultrasonic technologies are more useful than sonic technology but can cost more, as they can be more durable for machinery. Naturally, these technologies complement technicians' greatest instrument: the ears. Ultrasonic technology is an effective way to enhance a car's listening experience by detecting how the engine sounds or if the engine leaks.
Vibration Analysis Sensors
Vibration analyzer sensors detect vibration in components, detecting problems and the data is transmitted through a database for analysis. With a modern CMMS, one can observe changes over time through a comparison of current and previous data. In addition to a structured CMMS machine learning approach machine learning can be applied to a variety of fields of research.
Oil & lubricant sensors
Oil analyses are important in determining your machine's efficiency. Oil viscosity is the measure of a machine’s ability to protect against oxidizing dilution or moisture. Metal fragments in the oil may alert technicians to parts grinding that could cause problems. Sensory data can identify leaking connectors causing damage. Petroleum analytics software has existed for quite some time. Most modern car systems incorporate it within the central computers. Checking your vehicle's oil pressure and oil temperature are examples of predictive maintenance. This software system can be installed easily in existing machines.
Condition-Monitoring Sensors
The sensor system monitoring machinery is essential for predictive maintenance. Using sensor data, engineers assess machines' performance and wear in real time. This sensor can track maintenance needs from within the equipment without compromising operation. Many sensors define their functions and differ according to the type of machine. The parameters often use the vibrations and noise analysis, the pressure and oil analysis and sometimes the electrical current and corrosion analysis as inputs in a system.
Examples of condition monitoring in a manufacturing environment are:
Vibration monitoring: The vibration is observed to monitor the changes in the machine's condition.
Temperature monitoring: The temperature of the equipment is monitored to identify if there are any areas that are overheating or need more cooling.
Oil analysis: The oil levels and viscosity are checked regularly to ensure that the equipment is in optimal working condition.
Pressure monitoring: The pressure of the fluid or gas used in the system is monitored to ensure that it is at an acceptable level.
Electrical current analysis: The electrical current flow is analyzed to identify any issues with wiring or other components.
Corrosion analysis: The corrosion rate of metals is monitored to identify any damage or degradation of the material.
Visual inspection: A visual inspection is performed to check for any visible signs of wear or damage.
Acoustic emission analysis: The sound of the machinery is monitored to detect any abnormalities.
Other Technologies for Predictive Maintenance
Besides these techniques, facility operators can employ other tools, such as motor condition assessment detailing the operational and running state of motors, and current analyses, which determine changes in the tube walls of centrifuges. Borescope inspection, CMMS, data integration and monitoring are helpful for predicting maintenance. Although PdM technology is a very important tool, it's important to find a good solution to ensure a successful PdM campaign.
Which tools are used for predictive maintenance?
The answer to this question is as varied as the industries that use them. However, there are some common tools used in PdM campaigns, such as infrared thermography, vibration analysis and oil analysis. Infrared thermography measures the surface temperature of equipment or components; vibration analysis detects changes in the mechanical components of a system; and oil analysis helps monitor the wear and tear of equipment components.
Oher non-destructive testing methods such as eddy current testing and ultrasonic testing are also often used in a predictive maintenance program. All of these tools help identify potential problems before they cause expensive damage or downtime. Ultimately, success with predictive maintenance depends on finding the right combination of tools that best fit your company’s needs.
It is important to also have a solid process in place to ensure the data collected from these tools are analyzed and acted on in a timely manner. To do this, an effective PdM strategy should include regular maintenance checks and inspections, as well as creating preventative procedures for any problems that may arise.
The Internet of Things (IoT)
These sensors capture huge amounts of data and combine these data to create an enabling Internet of Things system. Predictive maintenance depends on a number of sensors connecting assets to central information stores. The hub can connect wirelessly or via cloud services. In such a central space assets can communicate, collaborate, analyze information or propose the best course for their actions. Using these tools is important in predictive maintenance.
What is a predictive maintenance IoT application?
Predictive maintenance lets manufacturers monitor equipment performance using real-time sensors. You will also understand past history, and current and anticipated equipment availability as a total measure of equipment effectiveness. The data collected from the sensors is used to predict potential problems and create proactive maintenance strategies.
Predictive maintenance IoT applications can be used in a variety of industries, such as manufacturing, energy, healthcare, transportation and logistics. These applications will help optimize processes, minimize downtime and increase productivity. Predictive maintenance also provides better insight into machine health than predictive maintenance as well as for preventive maintenance. In particular, the combination of different technologies and systems can ensure optimal machine conditions and performance.
In conclusion, Predictive Maintenance is a powerful tool that helps facility operators to monitor the condition of their equipment in order to anticipate failures or other issues before they occur. It uses multiple parameters such as temperature, vibration and power usage to determine the health of the equipment.
Predictive maintenance can be applied in a wide range of industries, from manufacturing and energy to healthcare and transportation. By taking proactive measures, facility operators can avoid costly repairs and maximize productivity. With predictive maintenance, companies can remain competitive in their industry by ensuring optimal machine performance.
Read more insights
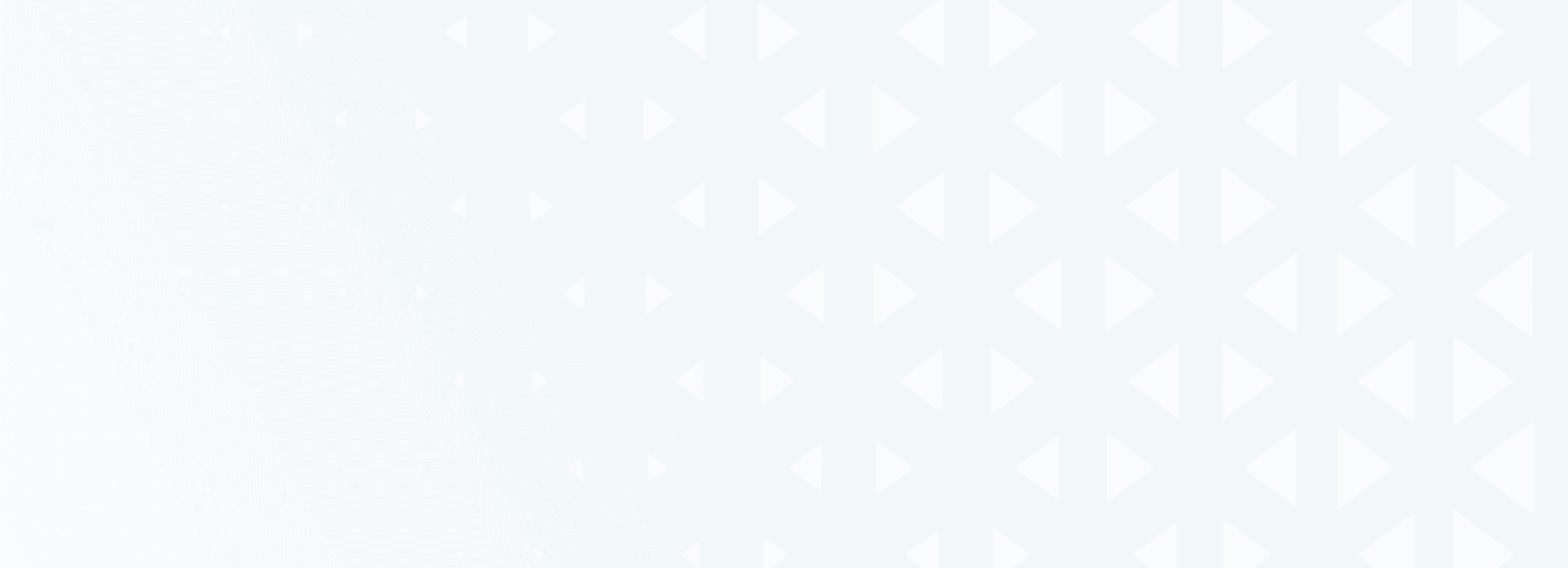